Combustion Engineering
ABOUT OUR RESEARCH
The Combustion Technology working group is dedicated to application-orientated basic research into combustion. In addition to investigating spray combustion in a rocket engine, the main focus is on fire safety in human spaceflight. In this field, experiments are carried out in the Bremen drop tower and in the GraviTower Bremen on sub-orbital sounding rockets, or in orbit, e.g., on the ISS. Extensive 1g tests are conducted in several facilities as reference data. On the other hand, numerical models for the simulation of flame propagation are also being developed on the basis of OpenFOAM.
Brand new findings on fire safety in space!
An internation science team used the Northrop Grumman Cygnus supply vehicle for the International Space Station to conduct experiments with large fires in space. Amazing data was transmitted from the return journey to Earth that even the combustion researchers could not have predicted. Florian Meyer explains that in weightlessness, a flame tends to spread in the opposite direction to the air flow. Accordingly, trying to blow out a flame on a spacecraft would be a really bad idea - if the blow off speed is not high enough.
Our fields of research
- Fire Safety in human spaceflight: Ground tests and microgravity experiments as well as simulations on the combustion of materials for space application.
- Droplet combustion: Experimental and numerical research on the combustion of single oxygen droplets in hydrogen.
- Droplet ignition: Experimental and numerical investigations on the auto-ignition process of hydrocarbon fuel droplets.
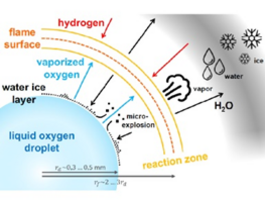
HYDRA I, Investiagion on the combustion of single LOX-droplets in hydrogen in microgravity
The goal of the project HYDRA is the investigation on the combustion of single liquid oxygen (LOX) droplets in a hydrogen environment under microgravity conditions. To enable these conditions an experimental setup is developed and integrated into a drop tower capsule. In parallel to the drop tower experiments the University of Washington develops a numerical combustion simulation and parametric studies will be performed to be compared with experimental results. Typical applications for hydrogen-oxygen combustion are rocket engines.
The main components of the experimental setup are the combustion chamber, which is sheathed by a liquid nitrogen (LN2) container and a vacuum container for insulation purpose. The combustion chamber is developed to withstand an initial pressure of >50 bar (supercritical).
The initial temperature will be 77 K by cooling with LN2. To generate a LOX droplet gaseous oxygen is poured into a cryogenic needle valve. Due to the LN2 sheath the oxygen condensates and is drawn into the combustion chamber when the valve is opened. A suspender is designed to allow the LOX to flow downwards and form a single droplet at the suspender tip, which is molded spherically to hold the droplet in position. In microgravity the droplet is ignited through a plasma discharge and the combustion is observed. Ambient pressure and the constitution of the atmosphere are the varied parameters.
Measured or diagnosed are: the droplet diameter through shadowgraphy, the instant of the flame and it’s diameter through OH-PLIF, OH-chemiluminescence and Schlieren optics, the temperature field information are derived from the density gradients visualized through the Schlieren optics.
Subcontractors/ project partners:
Leibniz-Institute of Photonic Technology, IPHT-Jena
University of Washington (UW), Seattle, USA
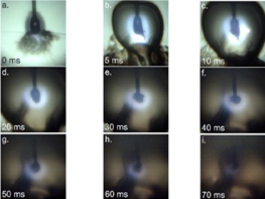
HYDRA II, Combustion of LOX-droplets in hydrogen and H2/He atmosphere at sub- and supercritical conditions
In the HYDRA II project, the same apparatus as in the HYDRA I project is being used to investigate the combustion of LOX droplets also in mixtures of hydrogen and helium, as well as combustion at high pressures in the supercritical range of oxygen. Where the droplet becomes supercritical, it loses its surface tension. One question is then whether the mixture formation and the subsequent combustion can proceed faster as a result.
The following quantities are to be determined in experiments under weightlessness:
Determination of the droplet diameter regression (using local high-resolution shadowgraphy method).
Determination of the flame radius and the distance of the flame from the droplet (by means of local high-resolution schlieren optics).
Measurement of the density gradient field, from which information about the temperature distribution around the droplet can be derived (using local high-resolution schlieren optics).
Measurement of OH concentration in line-of-sight (using recording of OH chemiluminescence, < 100 ms integration time).
In parallel, a simulation of droplet evaporation and combustion will be developed in collaboration with the University of Washington (UW). Using these simulations, validated by experiment, the steps toward simulating engineered spray combustion will then occur. Thereby, the transition to small droplets of technical dimensions and the inclusion of droplet interactions during combustion will be simulated. This will be done using methods developed for simulating the ignition of hydrocarbon sprays in previous projects.
Project partner:
University of Washington (UW), Seattle, USA
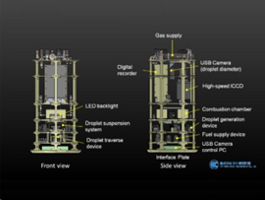
PHOENIX-II, Auto-ignition of groups of n-decane droplets in the cool-flame regime in microgravity
Effects of droplet and droplet group interactions during autoignition of n-decane droplets will be investigated on a TEXUS Sounding Rocket Mission in cooperation between DLR and ISAS.
Inside two furnaces of slightly different temperature (550 and 570 K) the effects of neighboring droplets on the autoignition will be examined during five subsequent experiments. The total number of experiments will thus be 10. The number of droplets and its relative position will be altered from experiment to experiment. Both temperatures are such low that the droplets are expected to ignite only in the cool-flame regime.
However, the induction times will be such long to enable a good temporal resolution of the ignition process and the slight kinetic differences. The ignition will be monitored by an intensified high-speed camera system that depicts the development of the formaldehyde concentration around and in-between the droplets. Formaldehyde is one important product of the cold combustion besides OH-radicals. While the concentration of OH is rather small during stable cool-flame combustion the concentration of formaldehyde will grow into the percent range. The Sounding Rocket flight is foreseen to happen in 2023.
The experiments are complimented by preparatory drop tower experiments as well as numerical simulations including full chemistry of the low temperature reaction branch. The development of the hardware will mainly be done on the Japanese side. Germany contributes the intensified high-speed camera and image data recording. The costs for the rocket flight will be covered by the German side. Airbus Defence and Space will be responsible for integration and flight execution. DLR-MORABA and OHB are contributing the rocket engines and telemetry and recovery systems.
Partners of the experimental team are:
- German Space Agency DLR, D
- Masao Kikuchi, Japan Aerospace Exploration Agency, JAXA, J
- Mitsuaki Tanabe, Hiroshi Nomura, Nihon University, J
- Osamu Moriue, Kyushu University, J
- Masato Mikami, Yamaguchi University, J
- Christian Eigenbrod, ZARM, D
The Project is supported by the German Aerospace Center, DLR and the Japanese ISAS
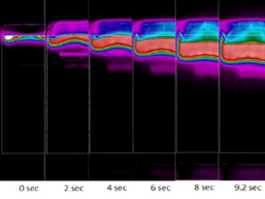
FLARE-G I, Flammability limits at reduced gravity
The determination of flammability limits of solid fuels in reduced gravity is important in efforts to increase fire safety in inhabited spacecraft. Flammability limits here do not mean the minimum and maximum fuel/air ratios, as is usually the case, but the range in which a fuel burns in a self-sustained manner in the dimensional field between oxygen concentration and flow velocity. If the flow velocity generated by the life support systems is too low, a fuel will extinguish even at very high oxygen concentrations (quenching). If the flow velocity is too high, a fire is blown off.
In drop tower tests on thin PMMA sheets (0.2 mm thickness), the parameters oxygen concentration, inflow velocity and test pressure are varied and the test results (flame propagation velocity and extinction limits) are compared with simulation results.
Different pressure/oxygen concentrations are used in astronautical spaceflight. These pairings can be varied along the so-called NORMOXIC curve without physiological deficiencies. Thereby the oxygen partial pressure is kept constant at 21.3 kPa. The limits of the curve are, on the one hand, normal conditions (101.3 kPa/ 21.3 % O2) and, on the other hand, the conditions that prevailed during the Apollo missions (21.3 kPa/ 100 % O2). Basically, it has been shown that decreasing pressure only slightly dampens combustion, while increasing oxygen concentration strongly commences combustion. Under conditions of high oxygen concentration, even materials qualified as fire-safe under terrestrial conditions (e.g., NOMEX and silicone) can burn self-sustainingly.
The project is integrated as an integral part of the international FLARE program coordinated by Japan's JAXA.
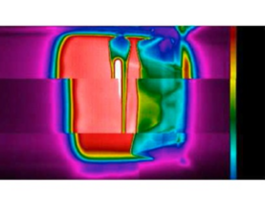
FLARE-G II, Flammability limits at reduced gravity – “Distributed Fuels”
Flames on solid fuels spread on the ground mainly with the flow. In microgravity, this is not the case. Due to the absence of buoyant convection, the flow remains stratified even through the flame. Thus, the flame protects the downstream region from oxygen ingress. As a result, a fuel can be heated under the flame and form large amounts of flue gas, but these are not ignited by the flame due to the lack of oxygen. So under normal gravity, flames can easily jump over fuel gaps. The question is, what about under microgravity conditions?
With flow, jumping is hardly possible because the base of the flame is stuck to the leading edge of a fuel and can only move downstream at the speed at which the leading edge burns off. Against the incoming flow, however, the propagation velocities between 1g and µg are not so different - at least quite slow (< 1mm/s).
Experiments in the same apparatus used for FLARE-G I will be used in FLARE-G II to clarify how flames jump over fuel gaps. These gaps can be either transverse to the direction of propagation or parallel to it with gradually decreasing gap width. Fuel gaps can be made of air, or of metal that is a good conductor of heat, or of materials commonly used in spaceflight that are generally considered to be fire resistant (e.g., Kapton , NOMEX, or silicone).
Again, inflow velocity, pressure and oxygen concentration play a role as they determine the power and shape of the flame base. Accordingly, these quantities are to be varied.
The project is integrated as an integral part of the international FLARE program coordinated by Japan's JAXA.
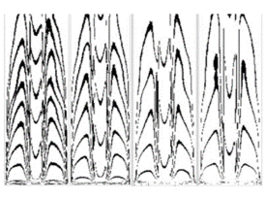
TOPOFLAME I, Effects of topography on flame propagation over solid fuels
In standardized flammability tests, which are carried out for space materials on the ground, flat material samples are to be examined. In contrast to this, however, it can be assumed both that the materials in real use are mostly structured and that flame propagation proceeds faster along edges, for example, than over surfaces. The reason for this is ultimately the lower heat capacity of a corner and the fact that the flame can heat up an edge from two sides. The same applies to grooves. If the groove is very narrow, a flame cannot ingress into it and the groove increases the surface into which the power is radiated. Thus, a narrow groove has a retarding effect. A wide groove, on the other hand, into which a flame can enter, consists of two opposite edges whose edge flames reinforce each other.
The TOPOFLAME I project is therefore investigating how surface structures influence flame propagation, especially under 1g conditions. For this purpose, an apparatus was built that allows these investigations in atmospheres of variable pressure and variable oxygen concentration. A balance on which the sample holder is mounted allows the mass loss during combustion to be determined. The burning can be studied both upward and downward, that is, with or against buoyant convection.
The results can help improve terrestrial fire safety as well as provide important insights for spacecraft design
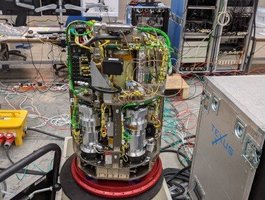
TOPOFLAME II, Sounding Rocket experiment on the flame propagation along cylindrical PMMA-samples at reduced pressure and enhanced oxygen concentration
The TOPOFLAME II experiment is the microgravity counterpart to TOPOFLAME I, in which mainly experiments, under 1g conditions were performed. Experiments on solid fuels of larger thickness require a lot of time as the propagation in microgravity is slow. Therefore, the TOPOFLAME II experiment is designed for the Sounding Rocket and has the flight number TEXUS 57.
The experiment consists of five cylindrical wind tunnels, all of which have laminar flow with a velocity of 20 cm/s. This velocity is comparable to the air velocities on board e.g. the ISS. The pressure in the ducts is 70 kPa and the oxygen concentration is 26.5 % O2. These values are on the NORMOXIC curve and are intended for future exploration missions. There are five cylindrical PMMA samples in the five channels whose diameters are 5, 10, 15, 20, and 25 mm. The samples are ignited at the upstream end. And the combustion is observed by IR and VIS cameras. In the exhaust gas stream of the five combustion chambers, the concentrations of O2, CO2 and the water content are also measured to obtain a full picture of the conversion rate.
In addition to the question of combustion conversion, it is also a question of what shape and length the flames have, what shape the sample tip assumes when stationary, and whether the flame breaks up in the region of the stagnation point. This is expected at least for the thicker samples, where the flow velocity should be too small to maintain the flame. All information used for the validation of numerical simulations.
The flight of the TEXUS 57 experiment TOPOFLAME is scheduled for 2022.
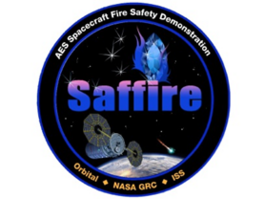
SAFFIRE, Spacecraft Fire Safety Experiments
SAFFIRE is the acronym for a series of NASA fire safety experiments on the unmanned ISS re-supply vehicle CYGNUS. Here, for the first time ever, realistically large samples of material (up to 1 m^2) are ignited with virtually no limiting containment. Typically when burning solid materials in space it requires several safety containments. As modules are standardized and thus limited in size, one ends up with rather small samples showing boundary effects. Since CYGNUS burns up anyway when it enters the atmosphere after undocking from the ISS, such extremely important large-scale experiments are risk-free. The experiment module, which is almost the size of a desk, consists of a wind tunnel with a sample holder mounted on its central axis.
During the various SAFFIRE flights, different samples made of different materials and with different geometries are studied while varying the flow velocity, pressure and oxygen concentration. The atmosphere is extracted from the spacecraft and returned to it after filtering.
In this respect, the contamination of the spacecraft is also interesting to follow. For this purpose, additional sensor modules are mounted in different positions of the spacecraft. If experiments are to be carried out under conditions other than those of the ISS, to which Cygnus was coupled, the pressure of the spacecraft can be released and the oxygen concentration increased by adding oxygen.
During the SAFFIRE V experiment, a PMMA sample was ignited at the downstream end and propagation against the inflow was monitored by cameras. The cameras allowed a view from the side as well as frontally on a surface. The sample with dimensions (W x L) 400 x 200 mm and an average thickness of 10 mm was equipped on both sides with vertical ribs of 1 - 10 mm width and a height of 3 mm. Horizontal ribs were provided for a concurrent flow test, which did not ignite and does not make sense in opposed configuration.
It was found that the narrower the rib, the faster the propagation, and that no mutual enhancement was observable above a rib width of 7 mm. The individual flames have an equal finite length and the "shadowing effect" prevents the flame front from spanning a burning surface behind.
The SAFFIRE series is funded by NASA and led by NASA-Glenn Research Center.

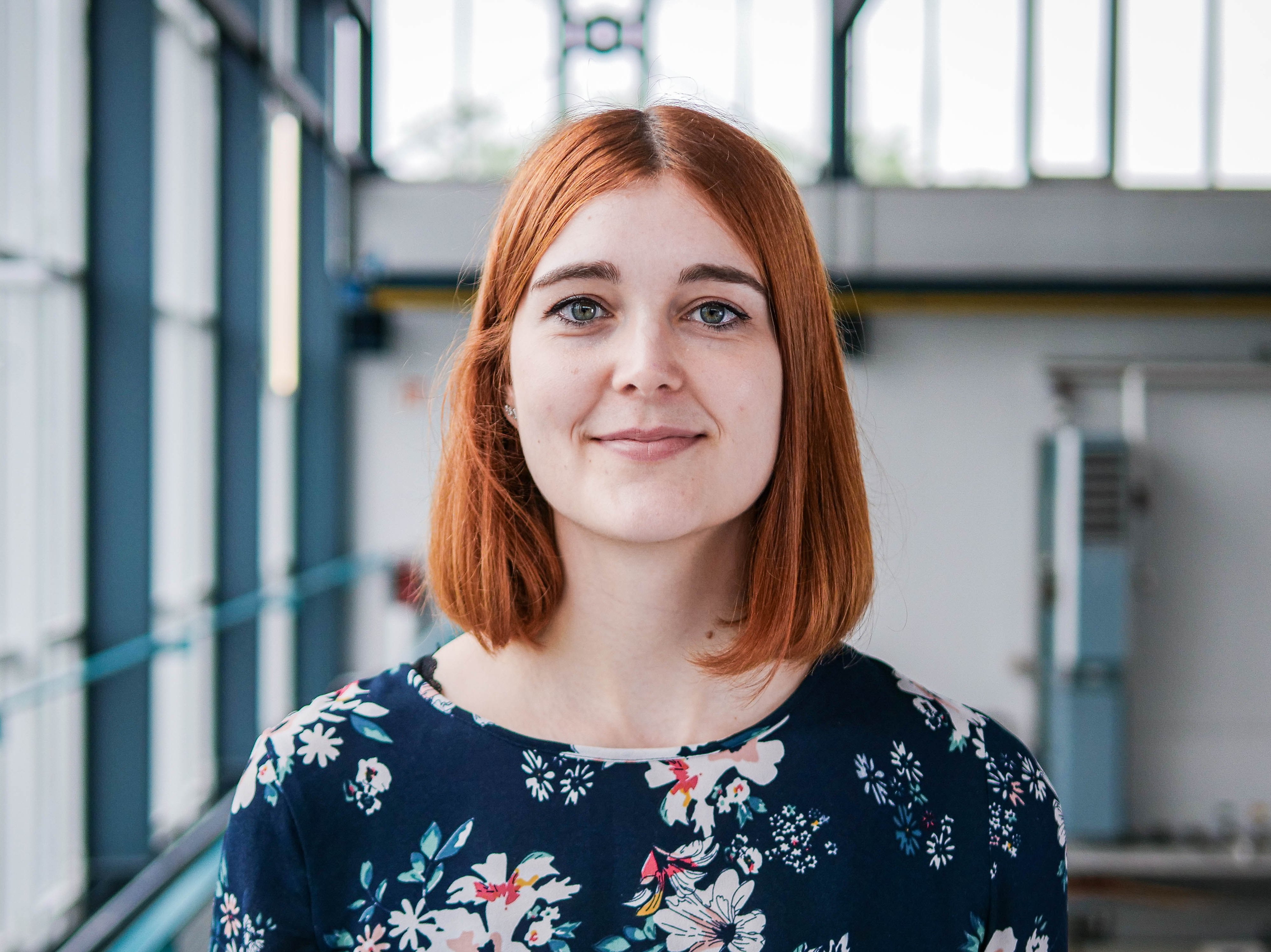
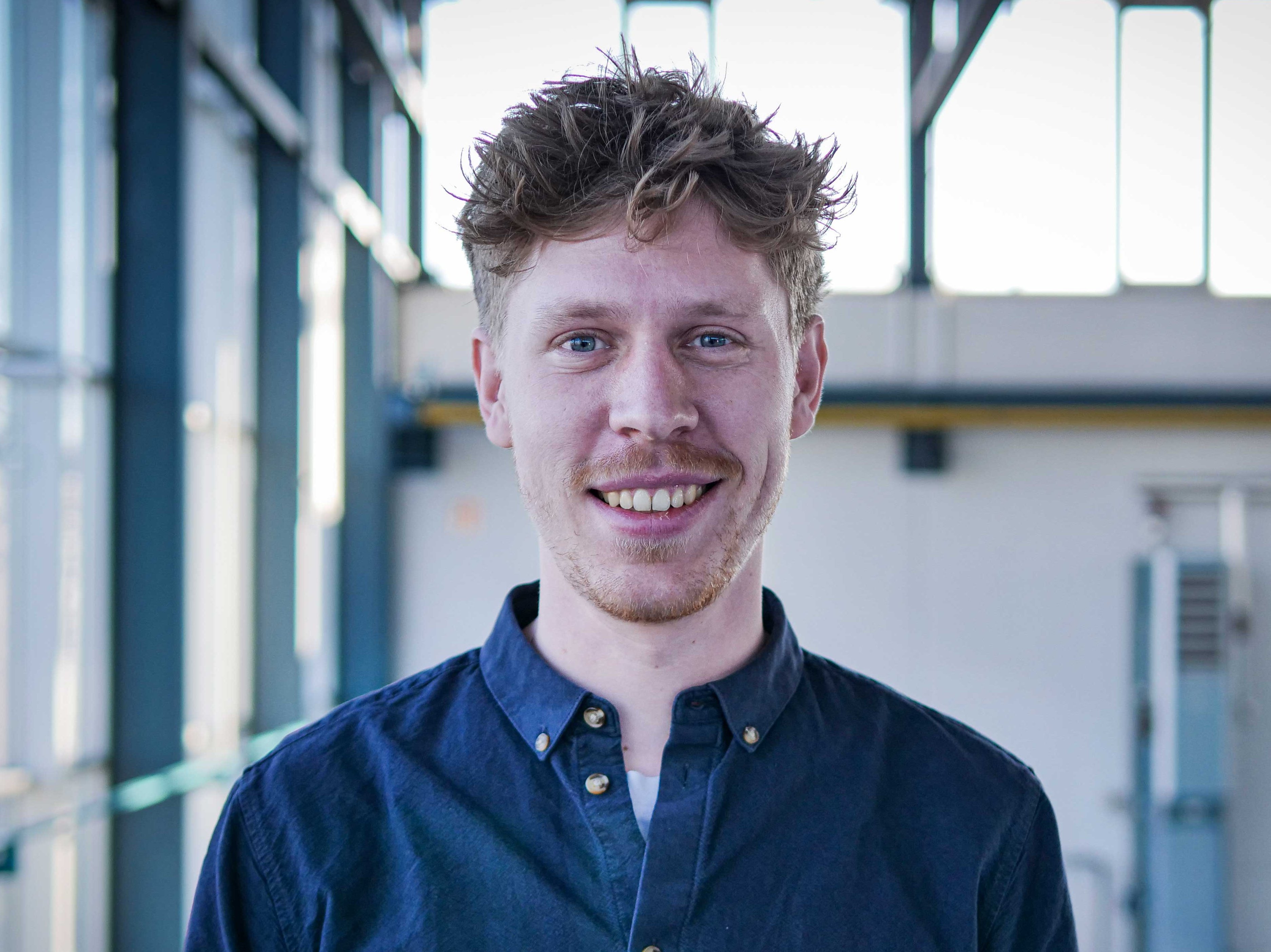
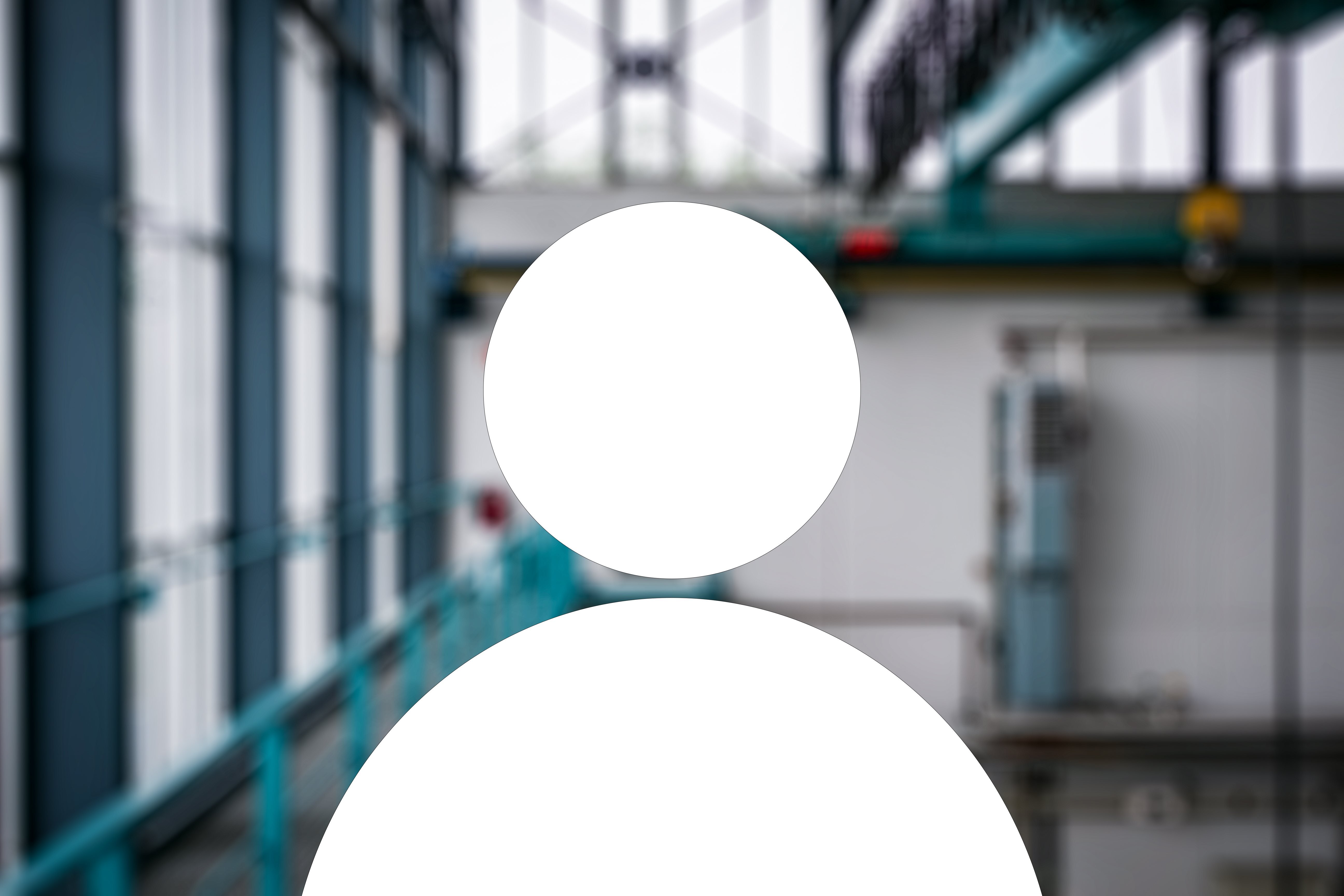
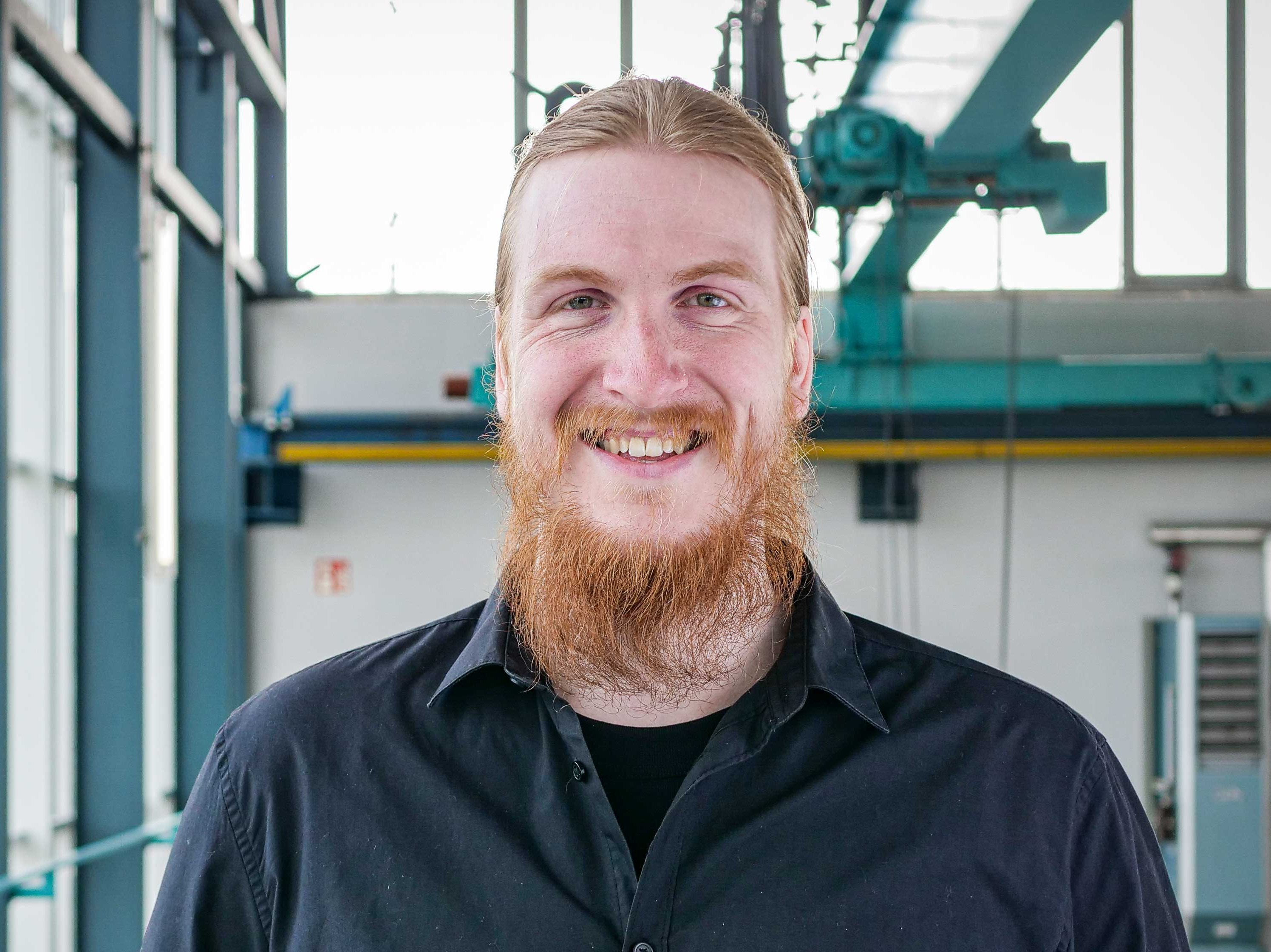

The list below shows the latest 25 publications of this research group. For the complete, searchable list of ZARM publications, please click more
2024
Development of a Pre-Ignition Fire Detection Sensor System
2024
Effect of oxygen concentration, pressure, and opposed flow velocity on the flame spread along thin PMMA sheets
Proceedings of the Combustion Institute, 40 (1) :105358
2024
Preliminary Results from the Saffire VI Experiment
2024
2023
Sooting Behavior in Concurrent and Upward Burning of Cylindrical PMMA-samples
2023
2022
Liquid oxygen droplet combustion in hydrogen under microgravity conditions
2022
Oxygen droplet combustion in hydrogen under microgravity conditions
Combustion and Flame, 241 (112081)
2022
2021
Combustion of Single Oxygen Droplets in Hydrogen under Microgravity Conditions
Volume AIAA 2021-0548
2021
Fire Safety Implications of Preliminary Results from Saffire IV and V Experiments on Large Scale Spacecraft Fires
2021
Opposed flame spreading along a structured PMMA sample in exploration atmosphere under microgravity
2021
Spontaneous ignition of droplet pairs of n-Decane and n-Tetradecane in microgravity
Volume 38
2021
2020
Apparatus to investigate liquid oxygen droplet combustion in hydrogen under microgravity conditions
Review of Scientific Instruments, 91 (105110)
2020
Combustion of Single Liquid Oxygen Droplet in Hydrogen under Microgravity Conditions
2020
2019
Concurrent Flame Spread Over Two-Sided Thick PMMA Slabs in Microgravity
Fire Technology, 56 :49-69
2019
2018
Analysis of Saffire II two-sided concurrent flame spread over a thick PMMA slab
2018
Fire Safety in Human Space Flight - Research for Improved Standards
2018
Microgravity Experiments and Numerical Simulations on the Combustion of Single Oxygen Droplets in Hydrogen
2018
Microgravity two-sided concurrent flame spread over a thick PMMA Slab
2018
2017
Experimental Findings on Flame Propagation along PMMA Samples in Reduced Gravity on REXUS 20 (UB-FIRE)
Volume 2017
2017
Experimental Results on the Effect of Surface Structures on the Flame Propagation Velocity of PMMA in Microgravity
Volume 2017
2017
Results of Large-Scale Spacecraft Flammability Tests
Volume 2017
2017
The Saffire Experiment: Large-Scale Combustion aboard Spacecraft
Volume 2017
2017
UB-FIRE Experiment Results on Upward Flame Propagation along Cylindrical PMMA Samples in Reduced Gravity
Volume 2017
2017
2016
Analysis and comparison of experimental investigations on the flame propagation along cylindrical and flat PMMA samples under normal and microgravity conditions
University of Bremen, M.Sc.
2016
Analysis of Experimental Findings to Investigate the Flame Propagation along Surface Structured PMMA Samples under Normal- and Microgravity
University of Bremen, M.Sc. thesis
2016
Formaldehyde LIF-Diagnostics of the Autoignition of n-Decane Droplet Pairs in Microgravity
Int. J. Microgravity Sci. Appl., 33 :330306-1-8
2016
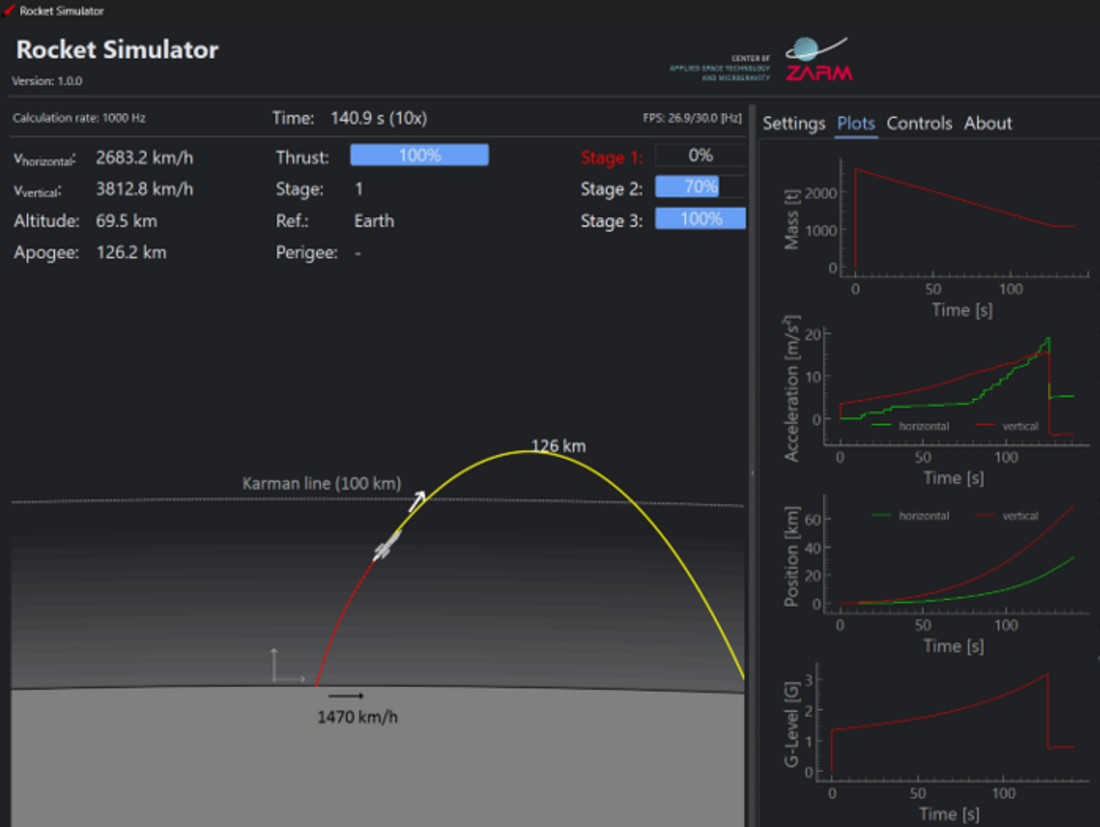
This is a simplified rocket simulator to test different rocket configurations. The model solves the rocket equation using the explicit Euler method. The density of the atmosphere is calculated up to an altitude of 85 km. Based on this, the atmospheric drag of the rocket or stage is calculated using a constant cw value. By conserving the angular momentum, simple orbit maneuvers can be performed. As an option, the Earth's rotation at the respective launch site can be taken into account for the orbit calculations.
Rocket Simulator: Download